Статья с канала «DL24 | История авто» на яндекс-дзене от 13 августа 2021 года.
Содержание:
Алюминиевый кузов — отнюдь не новинка XXI века, а скорее возврат к хорошо забытому старому: этот материал использовался в данной области ещё как минимум с 1920-х годов, пусть и не массово, а при штучном или малосерийном производстве автомобилей. Почему это делалось и какие при этом использовались технологии — в данной статье.
В своё время, просматривая ленту Дзена, я наткнулся на статью про автомобиль Bristol. В целом достаточно адекватную, правда, как обычно, воспроизводящую полуанекдотическую историю о том, что он происходит от довоенного прототипа BMW, что немного так преувеличение ) Но вот, про одну из основных особенностей этого автомобиля — то, что кузов его был сделан не из стали, а из «крылатого металла» — в статье почему-то не упомянуто вообще. А, между прочим, в те годы это был далеко не единичный случай — с тридцатых годов по середину пятидесятых использование алюминия и его сплавов для изготовления кузовов в автомобилестроении малых серий было очень и очень широко распространено. Так что его применение в кузовах современных автомобилей скорее следует называть возрождением старой, почти забытой технологии — пусть и на совершенно новом уровне.
В основном этот материал использовался при изготовлении кузовов люксовых или люксово-спортивных автомобилей, «кастомных» автомобилей (до того, как его стали использовать для продуктов тюнинга, это слово означало автомобили, изготовленные «с нуля» в единичных количествах), а также прототипов, шоу-каров и гоночных машин. «Алюминиевое» автомобилестроение сосуществовало с традиционным «стальным» в течение десятков лет, пока к середине пятидесятых годов на смену ему не пришла новая, более дешёвая и менее трудоёмкая технология изготовления кузовов из стеклопластика. Хотя в небольших количествах алюминиевые кузова по старинной технологии продолжали изготавливать и после этого, и делают вплоть до настоящего времени.
Примеры использования
Для начала давайте определимся с тем, о чём именно мы будем говорить в этой публикации. Дело в том, что алюминиевые кузова, как и любые другие, могут быть несущими или рамными; первые сами выполняют роль несущей системы, обеспечивающей прочность и жёсткость, а вторые — полагаются в этом отношении на отдельную раму. Так вот, серьёзно работать над несущими алюминиевыми кузовами начали только в последние десятилетия, они встречаются на ряде современных серийных автомобилей, вроде некоторых моделей Audi, Land Rover и Jaguar. К тематике данного канала — истории автомобилестроения и его технологий — они пока ещё отношения не имеют, и предметом данной статьи не являются:
Совсем другое дело — алюминиевые кузова, устанавливавшиеся на отдельную стальную раму: с ними начали экспериментировать чуть ли не с самой зари автомобилестроения. Самым первым вариантом были каркасно-панельные кузова, состоявшие из деревянного каркаса, обшитого отформованными вручную алюминиевыми панелями. Такими были, к примеру, кузова многих английских спортивных (и не очень) автомобилей двадцатых — тридцатых годов:
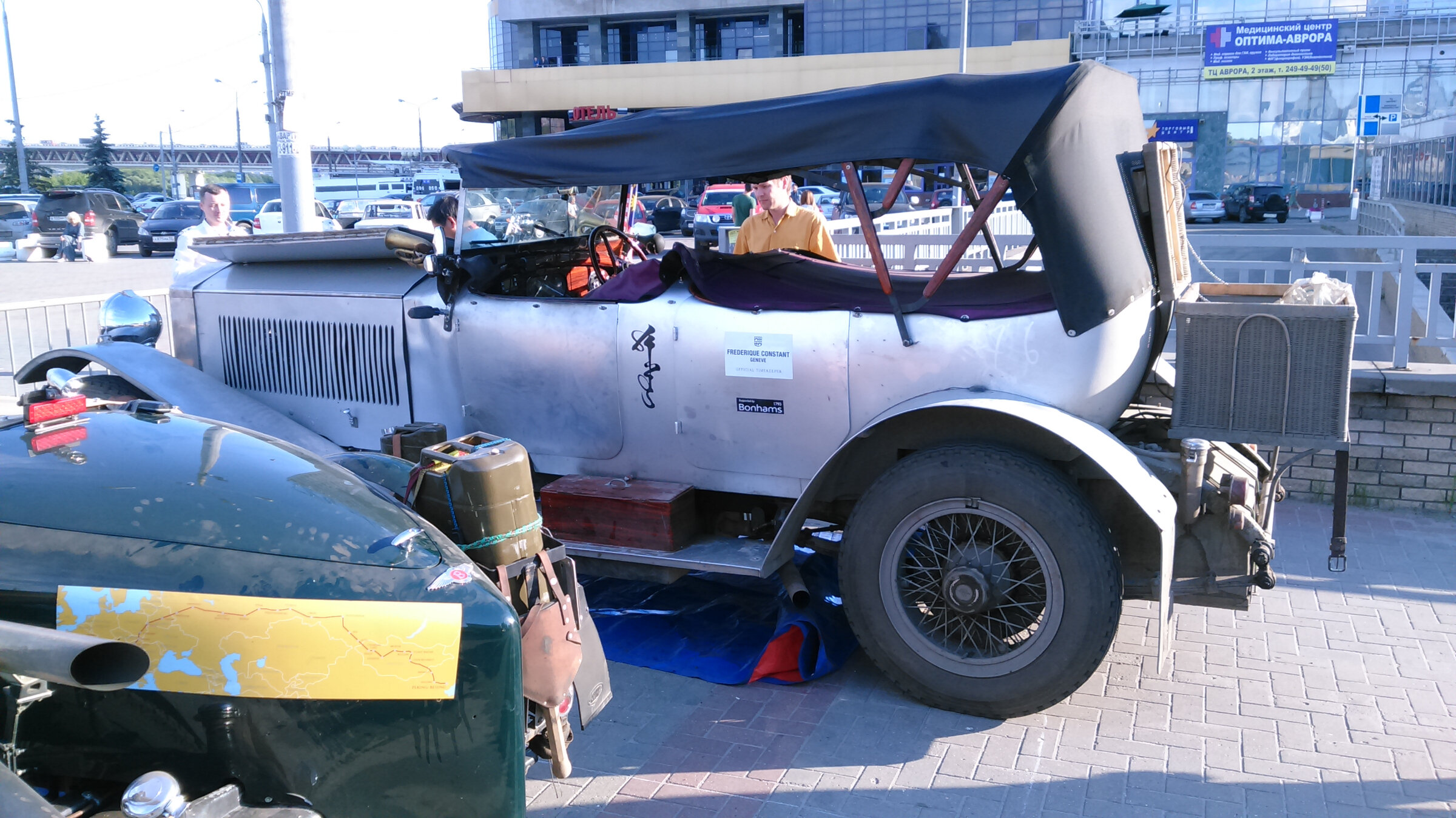
1931 Rolls-Royce Phantom II с деревянно-алюминиевым кузовом. Алюминий вообще часто не красили: и красиво, и видна вся крутизна как владельца машины, так и кузовщиков, построивших кузов с идеальной геометрией панелей безо всяких припоя и шпаклёвки. А если потускнел — всегда можно отполировать. Фото автора
Примерно по той же технологии вплоть до настоящего времени делаются английские автомобили Morgan. Между тем, начиная с середины тридцатых дерево вышло из моды в качестве материала для кузовостроения, и на смену алюминиевым кузовам с деревянным каркасом стали приходить новые их типы, например, кузова типа «суперлеггера» — сиречь «суперлёгкие». Как и исходит из названия, создавшие их в середине тридцатых годов итальянцы из ателье Carrozzeria Touring преследовали цель получить кузов, намного более лёгкий по сравнению с привычным, имевшим деревянный каркас, и при этом, в отличие от цельнометаллического стального, достаточно простой в изготовлении в условиях мелкой кузовной мастерской («карроцерии»).
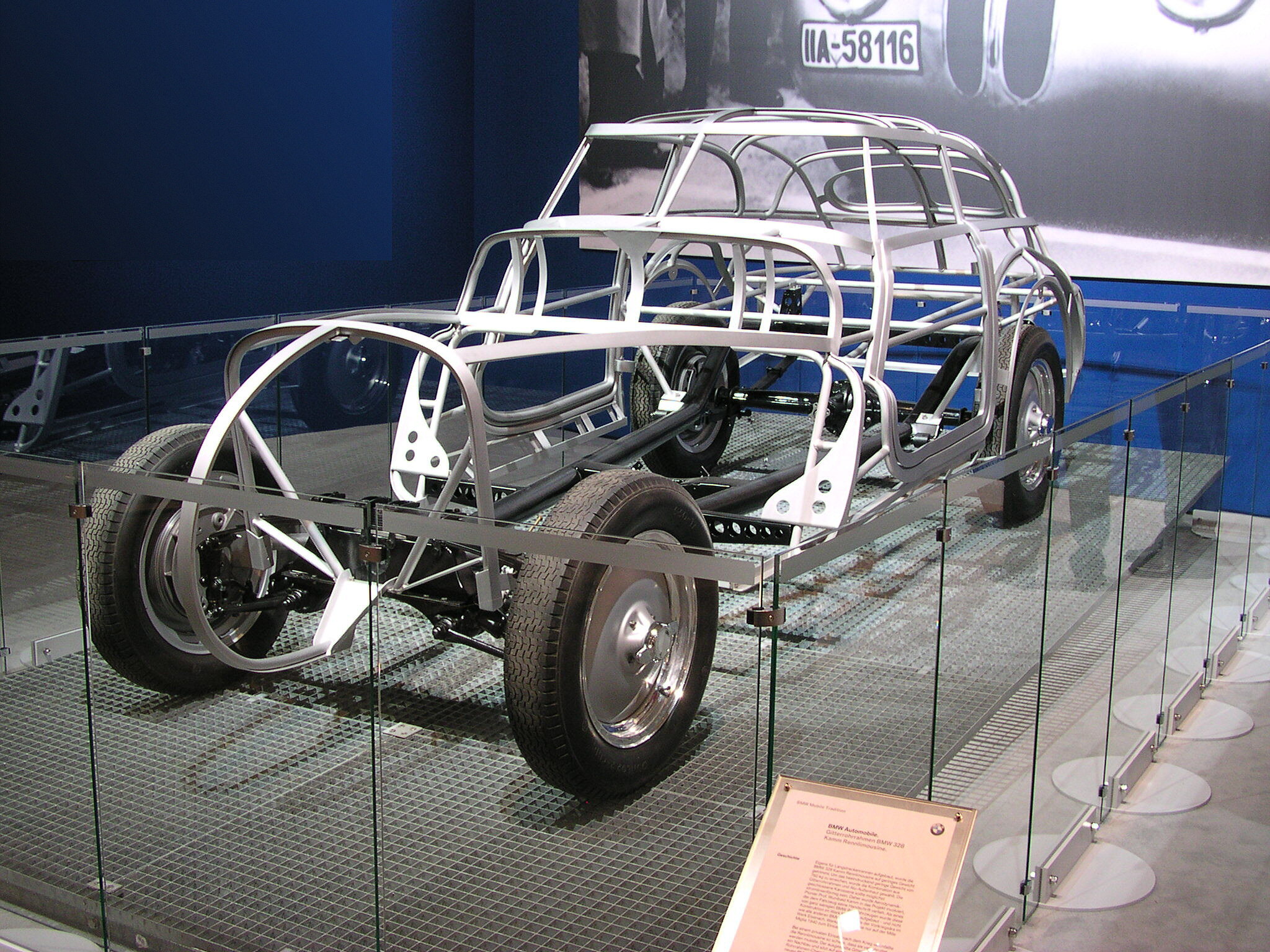
Довоенная BMW с единичным обтекаемым кузовом типа «суперлеггера». Как видно, этой технологией баловались не только итальянцы, но и немцы. Но суть от этого не менялась. Каркас кузова серебристый, а лонжеронная рама, на которую он установлен — чёрная. Фото: Википедия
Главная особенность кузовов «суперлеггера» — заменивший массивные деревянные балки относительно лёгкий стальной трубчатый каркас, который не нужно путать с пространственной рамой (рама у автомобилей с такими кузовами, как раз, в большинстве случаев самая что ни на есть обычная). А уже на этот каркас крепились алюминиевые панели, причём они как правило не прилегали к нему по всей площади, а лишь касались труб в нескольких точках (в том числе для предотвращения коррозии, так как гальванопара «железо + алюминий» имеет очень высокую электрохимическую активность). Именно так был построен кузов «Бристоля», с которого начался этот рассказ.
Наконец, существовали и «просто» алюминиевые кузова: которые как обычные стальные, но алюминиевые; как индивидуальной работы, так и массового производства. «Научное» название таких кузовов — «оболочковые», у них отсутствует отдельный от наружных панелей каркас, вместо чего прочность обеспечивается формой самой оболочки кузова, имеющей в нужных местах рёбра жёсткости и прочие усиления.
Такие кузова в стиле «ар-деко» до войны очень любили делать французы для своих малосерийных Delahaye, Delage и Bugatti. Но, пожалуй, всех затмил Габриэль Вузен — авиастроитель, после падения спроса на самолёты после Первой мировой войны переквалифицировавшийся в автомобилестроители. Его машины не просто имели алюминиевые кузова, изготовленные по авиационной технологии, но и всячески подчёркивали своё «небесное» происхождение за счёт очень характерного дизайна. Из всех именно Вуазен на тот момент ближе всего подошёл к концепции несущего алюминиевого кузова — у многих его автомобилей рама была объединена с основанием кузова. Впрочем, о «Вуазенах» уже много и хорошо написано на русском языке.
После Второй мировой войны алюминий и его сплавы какое-то время были неприлично дёшевы. Это подало многим автомобилестроителям идею использовать их и для кузовов массовых моделей. Например, по этому пути пошла французская фирма Panhard, выпустившая в 1954 году модель Dyna Z, изначально имевшую кузов из алюминиево-магниевого сплава Duralinox (близкий аналог отечественного дюралюминия), установленный на стальное несущее основание. Благодаря этому удалось добиться впечатляющих результатов: просторный и довольно комфортабельный автомобиль размером практически с нашу «Победу» весил в снаряжённом виде чуть больше 700 кг и с 40-сильным оппозитным двухцилиндровым моторчиком воздушного охлаждения, похожим по типу на двигатель мотоцикла «Урал», имел вполне приемлемую по тем временам динамику. Но и проблем у такого подхода было не меньше, чем достоинств.
Об этой машине и её непростой судьбе я уже рассказывал в статье в Википедии, повторяться не буду. Просто отмечу, что она была далеко не единственной в те годы, но из-за быстрого роста цен на «крылатый металл», основным потребителем которого была и остаётся авиация, от его широкого использования в массовом автомобилестроении пришлось отказаться на долгие десятилетия. Чуть ли не единственным исключением оказался британский «Ленд Ровер», которые в течение десятилетий использовал упрощённые клёпаные алюминиевые кузова на своих внедорожниках, но это совершенно отдельная тема.
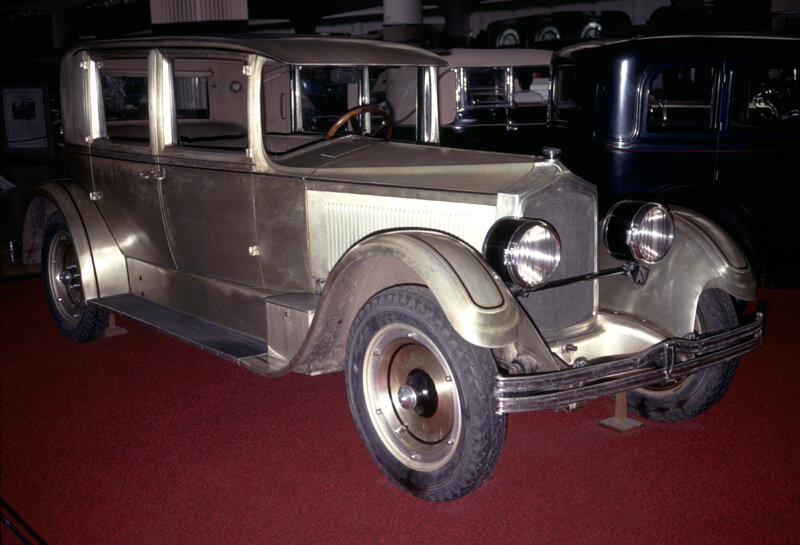
Опытный автомобиль с алюминиевым кузовом, совместно изготовленный ALCOA и Pierce-Arrow в середине 1920-х годов (один из, по разным данным, 16 или 18). Фото: https://gomotors.net/Alcoa-Pierce-Arrow/Alcoa_Pierce-Arrow-Sedan-_-Aluminum-Body/photos.html
Целый ряд штучных автомобилей с алюминиевыми кузовами был изготовлен и в довоенной Америке. Фирма Pierce-Arrow между 1912 и 1917 или 1918 годами даже отливала (!) из него кузова своих автомобилей. Большим апологетом этого материала для автомобильной промышленности были металлургические компании ALCOA и Kaiser Aluminum, изготовившие немало алюминиевых прототипов с целью демонстрации его возможностей.
Умели работать алюминием и у нас — например, из него изготавливались кузова спортивно-гоночных автомобилей, спроектированных авиационным инженером А. А. Смолиным, который использовал при этом привычную для него технологию. Собственно, принципиальной разницы между фюзеляжем или крылом самолёта и кузовом автомобиля с инженерной точки зрения по сути нет. Увы, но в 1967 году в советском автомобильном спорте произошли большие перемены: гоночный класс открытых автомобилей с произвольными кузовами был ликвидирован, вместо чего к гонкам были допущены переоборудованные серийные машины. Массовость соревнований, конечно, возросла, но зрелищность и техническая составляющая при этом сильно пострадали.
Причины использования
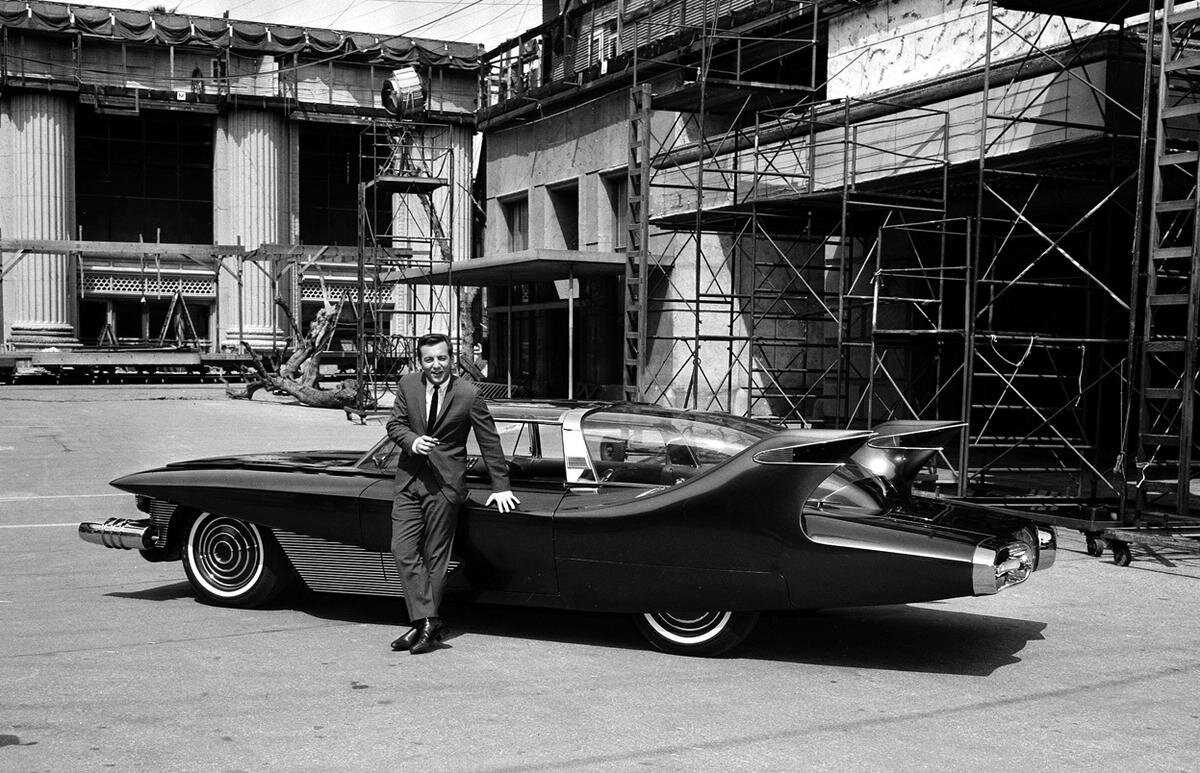
DiDia 150 — пример «кастомного» автомобиля пятидесятых годов с алюминиевым кузовом. К тому времени технология доживала свои последние дни в этой области — алюминий теснил более удобный в производстве пластик
Помимо лёгкости, огромным преимуществом алюминия и его сплавов была простота в обработке. Мягкий алюминий очень хорошо тянется, при наличии навыка ему достаточно легко придавать требуемую форму при помощи самых простых ручных инструментов, что позволяло изготавливать кузова, внешне почти не уступавшие заводским, практически буквально «на коленке». Именно поэтому алюминий был выбором номер один при изготовлении единичных экземпляров автомобилей, а также у всевозможных «самодельщиков». Во всяком случае, так было до появления ещё более дешёвой, и при этом намного менее трудоёмкой, технологии изготовления кузова из стеклопластика, которая сделал этот процесс доступным уже даже не маленьким мастерским, а работающим в одиночку «гаражным умельцам». Оснастка для малосерийного изготовления алюминиевого кузова тоже всегда стоила намного дешевле, чем для стального, что позволяло наладить выпуск автомобиля в небольших количествах с минимальным затратами.
Как они это делали?
Краткий ответ на этот вопрос, который я уже дал в комментариях к упомянутой выше статье про «Бристоль»: руками ) Здесь распишу уже более подробно.
Первый из описываемых технологических процессов был задействован в маленьких мастерских и у индивидуальных изготовителей «кастомных» автомобилей. Собственно, в случае единичного изготовления кузовов работа со сталью и алюминием имела довольно мало отличий, но алюминий требовал меньших трудозатрат и позволял получать более сложные формы, поэтому очень многие изготовители «кастомных» автомобилей в тридцатые-сороковые годы работали именно с ним.
В первую очередь, на основе сделанных дизайнерами чертежей и масштабных моделей строилась деревянная мастер-модель будущего кузова, воспроизводящая его форму во всех её нюансах. В некоторых случаях она могла быть сплошной, но очень часто мелкие производители ограничивались «скелетной», построенной из фанерных листов со сплошными деревянными вставками только на участках с особо сложной геометрией. Вопреки имеющемуся заблуждению, листы металла почти никогда не выколачивали прямо на поверхности мастер-модели: она служила в основном для проверки их формы и взаимной подгонки отдельных панелей друг к другу. Чтобы готовый кузов можно было снять с неё, мастер-модель как правило выполнялась разъёмной.
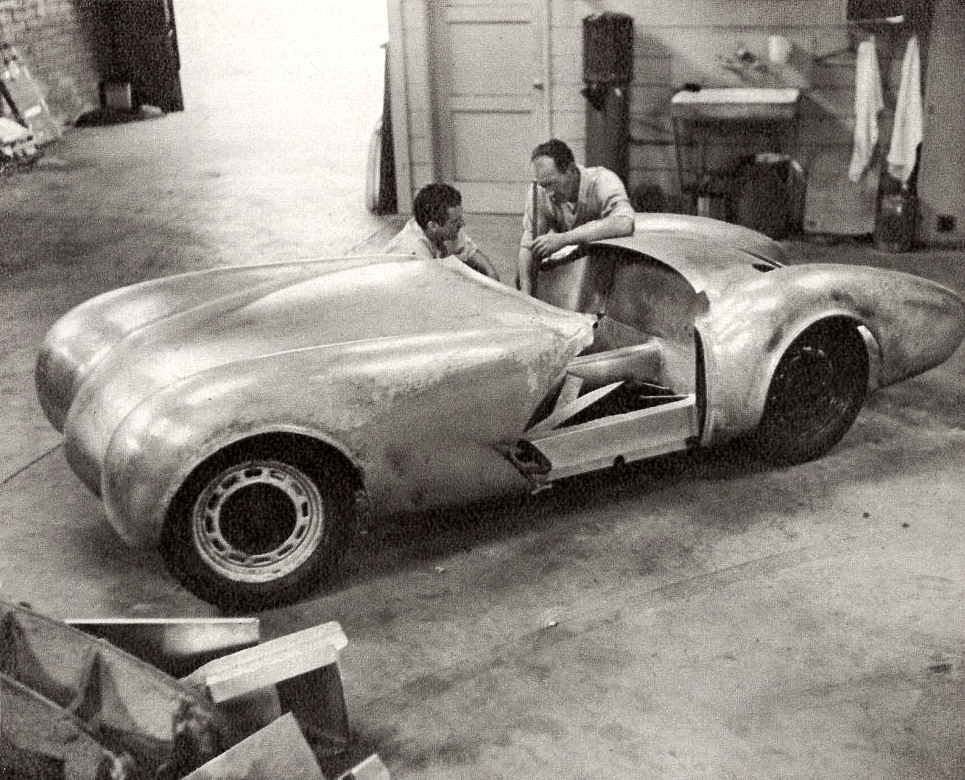
Кузовщик Эмиль Дейдт и дизайнер Винс Гарднер в процессе работы над «кастомным» автомобилем с алюминиевым кузовом. Из книги How To Build Hot Rods 1952 года издания
В некоторых случаях при изготовлении единичных кузовов могли не делать и мастер-модели, вместо чего для подгонки панелей использовали тот же каркас, на котором им предстояло быть установленными. При масштабе же выпуска в десятки или сотни автомобилей появлялся смысл в изготовлении специализированной оснастки, обеспечивающей повторяемость формы кузова от одного экземпляра к другому.
Форму предварительно отожжённым листам алюминия придавали вручную, преимущественно при помощи выколотки (дифовки) и осадки. Выколотка осуществлялась деревянными и стальными молотками на твёрдых оправках или мягких кожаных подушках, заполненных песком или дробью. Этим методом, не первый взгляд кажущимся попросту варварским, при должном умении удавалось получать очень сложные пространственные формы.
Также для вытяжки, осадки и рихтовки металла мог использоваться целый ряд инструментов, самым эффективным из которых считается так называемое «английское колесо» (роликовый вытяжной станок). Все основные использовавшиеся при штучном изготовлении алюминиевых кузовов техники работы с металлом показаны в приведённых выше видео.
В более крупных мастерских могли использоваться стационарные пневматические молоты и другие станки, значительно ускорявшие работу над кузовом, но не менявшие её сущности:
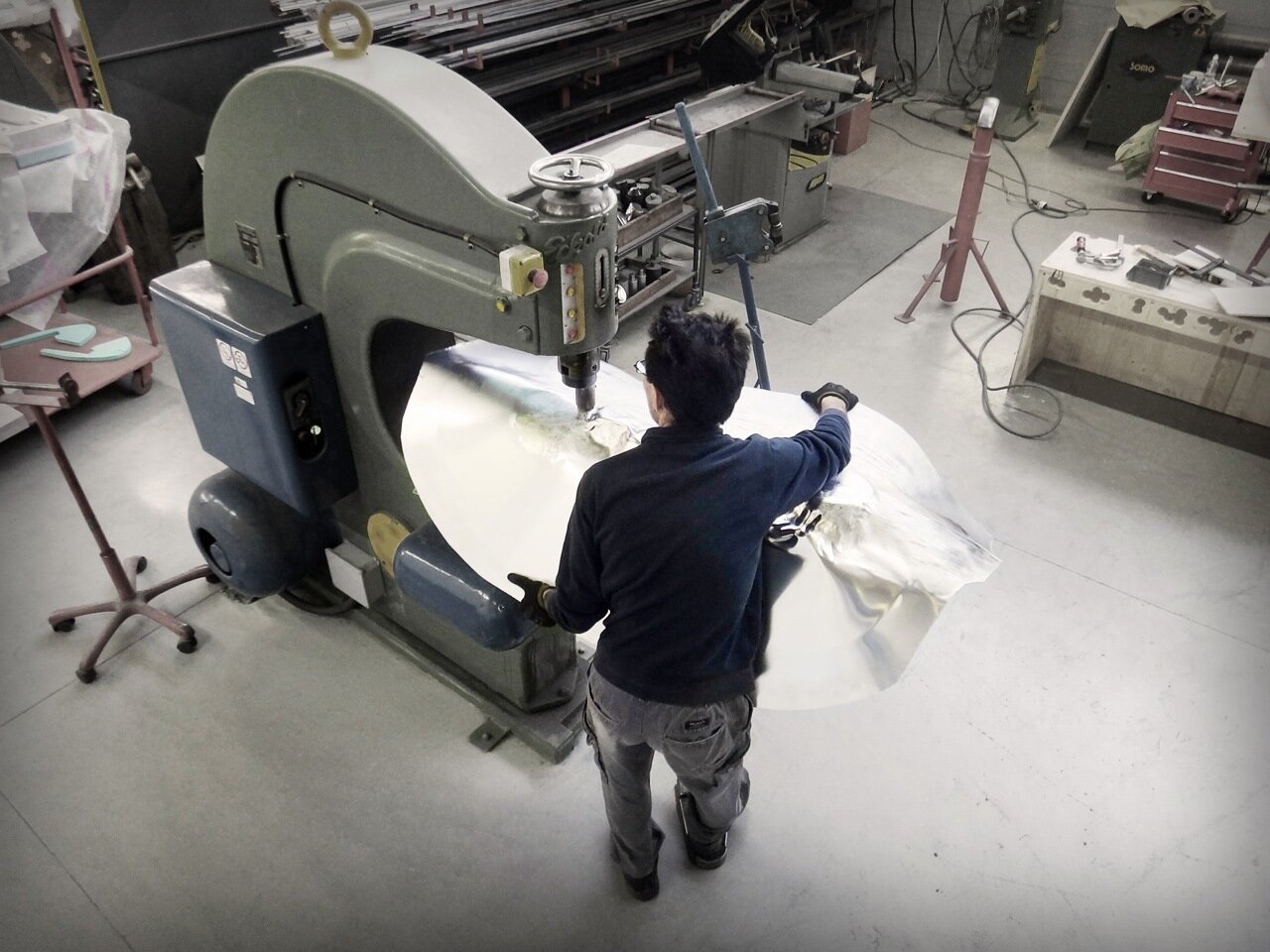
Использование пневматического молота для формования кузовной панели (в данном случае — панели приборов). Фото: Mini
Так как все работы при этом производились вручную, размер обрабатываемых панелей оказывался небольшим, и поверхность кузова приходилось составлять из множества отдельных «кусочков», причём их делали с «припуском» в несколько сантиметров, в расчёте на окончательную подгонку. После того, как все части кузова были готовы, их устанавливали на мастер-модели или заранее изготовленном трубчатом каркасе, зажимали струбцинами и подгоняли по месту так, чтобы листы идеально стыковались друг с другом практически без зазоров. Делалось это потому, что их сваривали «в стык» при помощи газовой сварки — а для этого было необходимо, чтобы кромка одного листа точно совпадала с ответной кромкой другого.
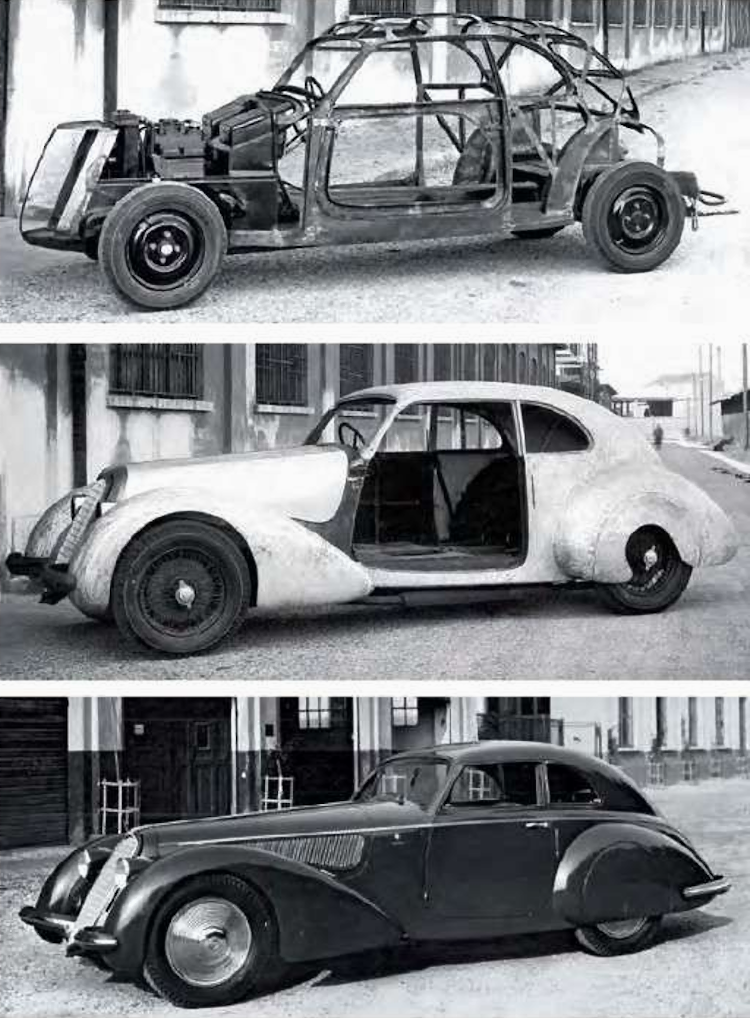
Различные стадии изготовления алюминиевого кузова типа «суперлеггера». Из книги Giovanni Bianchi Anderloni, Carrozzeria Touring Superleggera
Оставшиеся от сварки швы рихтовали до полного разглаживания наружной поверхности. Естественно, при сварке сплошным швом панели «вело», и они требовали рихтовки и дополнительной подгонки. Но при малых объёмах выпуска большой проблемы в этом не было. Сегодня при изготовлении «кастомных» алюминиевых кузовов часто используется TIG-сварка в среде аргона — дающая меньшее коробление деталей, но при этом и менее производительная. После сварки и зачистки швов кузов рихтовался, шпаклевался, грунтовался (как правило, теми же материалами, которые использовались в авиастроении) и окрашивался (уже по-автомобильному, обычно нитроэмалью во много слоёв с промежуточной шлифовкой каждого).
Данная технология, выглядящая довольно просто на словах, на практике была исключительно сложной и трудоёмкой, требовала от исполнителя виртуозного владения техникой обработки металла. Её нюансы работники кузовных ателье постигали в течение многих лет. Особенно сложным было изготовление кузовов, которые оставались без окраски — это требовало безупречного качества поверхности.
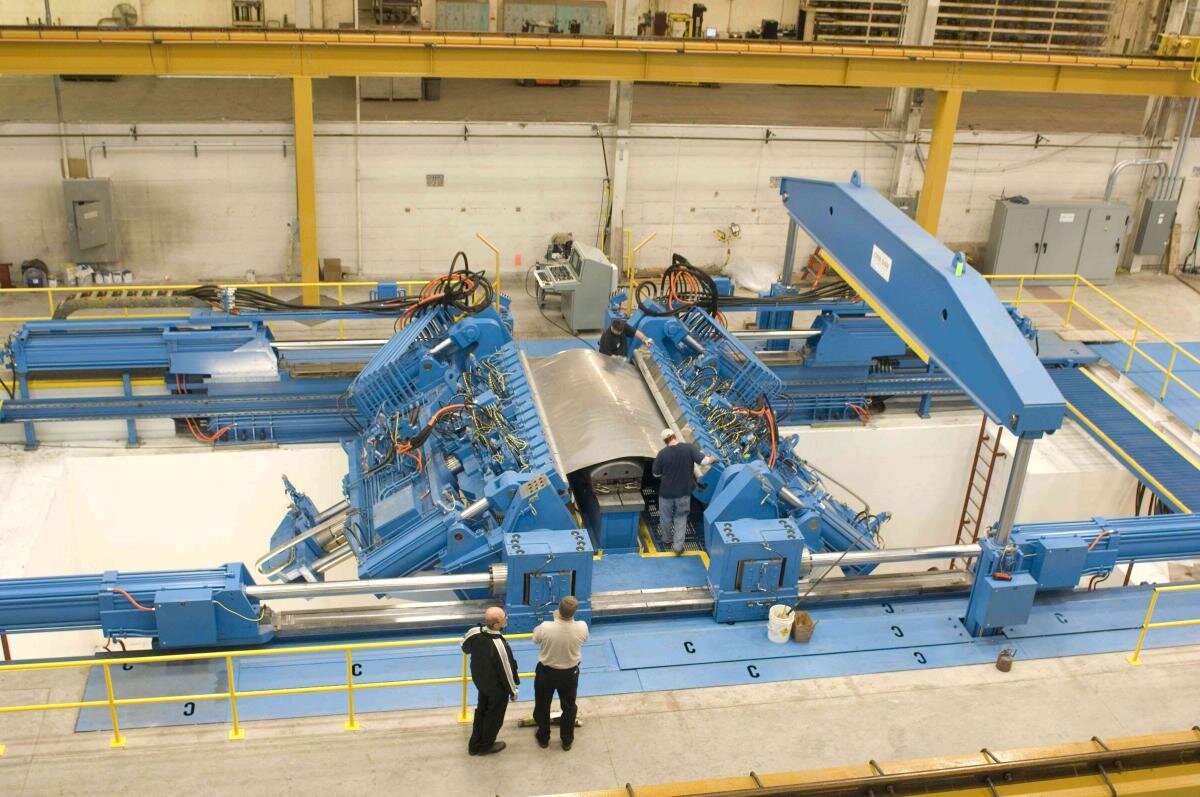
Обтяжной пресс в работе. Это кадр с авиазавода, но в малосерийном производстве алюминиевых автомобильных кузовов используются очень схожие технологии, только прессы размером существенно меньше
В малосерийном производстве обычно использовалась другая технология, позаимствованная, как и практически все приёмы работы с листовым алюминием, из опыта авиационной индустрии — формовка кузовных панелей на обтяжных прессах. При этом алюминиевый лист, находящийся благодаря предварительному растяжению в состоянии сверхпластичности, в самом буквальном смысле натягивается гидравлическими домкратами на деревянную, металлическую или пластиковую болванку (форм-блок):
Очень много операций, впрочем, всё равно приходится производить вручную — например, края панели обстукивают при помощи молотков, обеспечивая плотное прилегание металла к болванке и формируя торцы. Кроме того, такая технология не позволяет получать выпукло-вогнутые детали сложной формы — вогнутые участки приходится формовать по-старинке, ручной выколоткой при помощи оправки и молотка. Срок жизни деревянного форм-блока сравнительно невелик, но достаточен при масштабах выпуска порядка десятков или сотен кузовов в год, а его замена не стоит больших денег.
Именно так, к примеру, изготавливаются кузова реплики Shelby Cobra, выпускаемой фирмой Kirkham Motorsports, с техпроцессом которой можно подробно ознакомиться в документе по ссылке. Хотя данный процесс уже требует довольно существенных вложений в производственное оборудование, всё же оснастка для него обходится гораздо дешевле, чем полноценное прессовое хозяйство, необходимое для изготовления стального кузова. Сегодня получают распространение подобные прессы с ЧПУ, у которых поверхность болванки формируется при помощи матрицы из отдельных стержней — это делает производство более гибким и исключает трудоёмкий процесс изготовления целого комплекта болванок, позволяя быстро перестраивать производство и оперативно менять форму кузовных панелей.
В массовом производстве, естественно, использовались уже полноценные штампы с матрицами и пуансонами, и технология мало отличалась от используемой при производстве обычного стального кузова. Хотя тоже имела свои нюансы, вроде используемых методов сваривания.
Конец эпохи
К концу пятидесятых годов эпоха алюминиевых кузовов «старой школы» на легковых автомобилях подошла к своему концу.
В Европе после войны традиция изготовления дорогих машин с индивидуальным дизайном практически умерла, следуя за общей демократизацией общества и тенденцией к потреблению продуктов массового производства со стандартным дизайном. Кроме того, большинство производителей автомобилей перешло на несущие кузова, а это практически не оставило места для традиционного поля деятельности кузовных ателье — изготовления уникальных кузовов для установки на заводские «голые» шасси.
Большинство итальянских «карроцерий» к началу шестидесятых переквалифицировалось в дизайнерские бюро, которым автомобильные фирмы заказывали дизайн для серийных моделей, изготовление прототипов и шоу-каров. Дольше других продержались англичане. Одним из последних серийных автомобилей с кузовом типа «суперлеггера» был Aston Martin DB5, который выпускался в Англии с использованием купленной у Carrozzeria Touring Superleggera технологии. Правда, не так давно старую технологию возродили для постройки концепта Mini Superleggera Vision.
В Америке изготовление «кастомных» автомобилей «пошло в народ» — благодаря появлению стеклопластика в пятидесятые годы построить свой автомобиль с уникальным дизайном стало возможно в любом гараже. Вторым направлением «кастомайзинга» стал тюнинг кузовов серийных автомобилей, что подразумевало работу со сталью. С алюминием же продолжило работать лишь небольшое число мастеров.
Сильнейший удар по алюминиевым кузовам нанесло также широкое распространение дорожной соли начиная с шестидесятых годов, которая провоцировала быструю коррозию алюминиевых сплавов, и защищать их от неё в те годы толком не умели. После этого повседневная эксплуатация автомобилей с алюминиевыми кузовами в странах со снежной зимой оказалась под большим вопросом — во всяком случае, до появления методов надёжной защиты их от коррозии. И да, если вы считаете, что алюминиевый кузов не подвержен коррозии — вас ждёт жестокое разочарование: во всяком случае, для классических автомобилей с алюминиевыми кузовами это не соответствует действительности. При неподходящих условиях хранения гнили такие кузова довольно сильно, во многом из-за несовершенства тогдашних технологий, которые не позволяли достаточно тщательно изолировать друг от друга алюминиевую обшивку и стальные детали. Это приводило к тому, что в присутствии воды в месте контакта деталей из различных металлов друг с другом алюминий довольно интенсивно разрушался, превращаясь в белые рыхлые хлопья.
Были у них и другие эксплуатационные недостатки, например высокая склонность к образованию вмятин, сложность и дороговизна в ремонте.
источник: https://dzen.ru/a/YROgwfAO6jCi5oWM